Breakthroughs in battery research often put traditional lab tools to the test, and sample containers face new risks during thermal analysis. Safety and precision become bigger concerns with every innovation.
Recent improvements in battery technology have pushed thermal analysis sample containers to evolve quickly. Manufacturers and laboratories now work together to design safer, more robust, and specialized containers that meet the demands of new battery chemistries and high-energy testing.
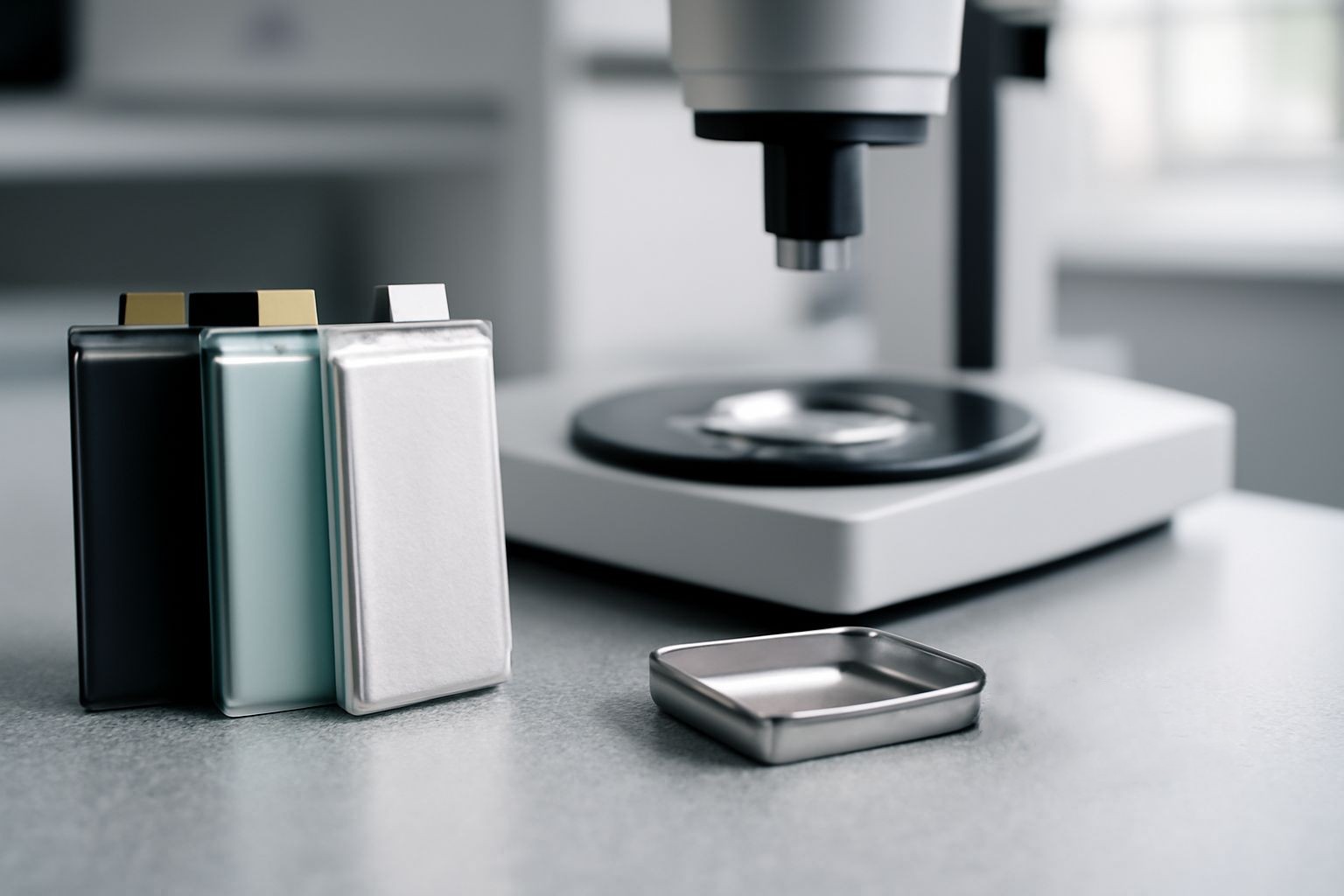
I have seen the battery industry grow fast in recent years. With each step forward—whether in solid-state designs or new electrode materials—come new risks in thermal testing. These changes force us to rethink container selection, durability, and how labs and manufacturers cooperate. Let us look at the main challenges and how the market now responds.
New Challenges in Sample Analysis?
Modern battery research introduces both aggressive chemistries and higher energy outputs. Standard containers no longer handle every risk as they did before.
Advanced batteries can react violently during thermal analysis, making stability and containment the top priorities for sample containers. Specialized designs and robust sealing are needed for safety and reliable results.
Specific Risks and Market Trends
Every newly launched battery brings different issues to the lab. Lithium-ion and solid-state batteries both require careful handling due to thermal runaway and high reactivity. According to recent research, container failures during high-temperature tests now occur more often, leading to stricter safety protocols and the development of new sample holders. This table breaks down the typical challenges found in battery analysis labs.
Battery Type | Main Thermal Challenge | Container Weak Point | Required Feature |
---|---|---|---|
Lithium-ion | Risk of thermal runaway | Seal can leak gases | Gas-tight, robust lid |
Sodium-ion | Reactive at moderate heat | Corrosion of pan | Chemical resistance |
Solid-state | High heat, unknown byproducts | Poor material compatibility | Ceramic or custom pans |
Lithium-sulfur | Sulfur vapor release | Leakage or contamination | Hermetic/vented design |
Source: Nature Energy - Battery Thermal Events Study
Adapting Container Materials for Battery Research?
Old materials like basic aluminum can no longer protect samples against aggressive battery chemistries or high test temperatures.
Modern battery analysis now uses high-purity aluminum, platinum, or ceramic containers. These materials resist both thermal shock and chemical attack, ensuring safer, more accurate measurements during testing.
Material Selection and Engineering Response
In my work with battery labs, I often recommend switching to alumina or platinum containers. New batteries, such as lithium iron phosphate, will corrode or even destroy basic sample pans. Ceramics block unwanted reactions and hold up under extended TGA or DSC runs. Many designers also now add features like pressure-resistant lids or integrated vent holes. The table compares key material properties matched to battery research needs.
Material | Max Temp (°C) | Corrosion Resistance | Heat Stability | Lab Use |
---|---|---|---|---|
High-purity Aluminum | 650 | Limited | Good | Standard batteries |
Alumina | 1600 | Excellent | Very High | Solid-state/advanced |
Platinum | 1650+ | Very High | Excellent | Problematic chemistries |
Ceramic composites | 1400 | High | Excellent | Specialty new chemistries |
Technical background: Thermal Analysis in Materials Science
Collaborations Between Battery Manufacturers and Analytical Labs?
No single group can solve the complex issues found in battery research alone. Strong partnerships now drive innovation in thermal analysis containers.
Battery producers and testing labs are working together to design custom sample holders that address specific research needs. These collaborations have produced new sealing technologies, vented containers, and data-driven improvements in container reliability.
Examples of Partnership and Innovation
I recall one case with an automotive battery maker and a national lab designing new vented pans to safely analyze high-energy pouch cells. Such efforts speed up the introduction of containers that match evolving battery chemistries. Open scientific exchange and testing feedback, as described by the ARPA-E battery initiative, have delivered better safety and measurement accuracy. The table outlines recent collaboration outcomes.
Partnership | Challenge | Solution | Benefit |
---|---|---|---|
Lab + Battery OEM | Thermal runaway risks | Pressure release/venting pans | Safe, repeatable tests |
Material supplier + University | Corrosive electrolytes | Ceramic-lined holders | Longer pan life, less error |
Tech start-up + Testing service | Pouch cell swelling | Expandable pan design | Fit new battery types, reduce failure |
Multi-lab network | Standards for data sharing | Standardized container specs | Reliable cross-lab results |
Reference: ARPA-E Battery Research Partnerships
Future Directions in Thermal Analysis for Battery Technology?
Future batteries will only get more complex. The next generation of sample containers must match this pace in safety, function, and data quality.
Next steps for thermal analysis sample containers include smart sensors, automated data tracking, and new composite materials. These changes support advanced battery testing and help prevent unexpected failures in both research and production.
Emerging Trends and Opportunities
I see more labs asking for integrated sensors that monitor gas release and heat inside the pan during real time. This step cuts risk and supports machine learning analysis of battery events. Smart labeling, such as RFID tags, enable traceable sample identity and storage of test data. New composites and engineering bring options like multi-layered pans with vented or self-healing coatings. The table lists future trends now visible in the battery testing world.
Innovation | Key Device | Benefit | Market Impact |
---|---|---|---|
Integrated temperature/gas sensors | Smart pans | Live feedback, safety | High for R&D, OEMs |
RFID/Smart labeling | Tagged holders | Traceability, auto-data | Boosts lab automation |
Vented/self-healing coatings | Protective novel pans | Less pan failure, better safety | Reduces downtime |
Multi-material composite pans | Hybrid containers | Customization for new chemistries | Fits new battery lines |
Forecast: MarketsandMarkets Battery Technology Report
Conclusion
Batteries evolve rapidly, and so must the tools we use to test them. The future of battery research depends on reliable thermal analysis containers that keep pace with new discoveries and industry demands.
Contact REDTHERMO for thermal analysis container solutions