Many labs struggle with unreliable test results and wasted samples. Picking the wrong crucible can lead to expensive mistakes and lost project time.
To find the best DTA crucible, choose a product that matches your instrument, uses quality materials, and is backed by clear supplier support. This approach delivers reliable lab results.
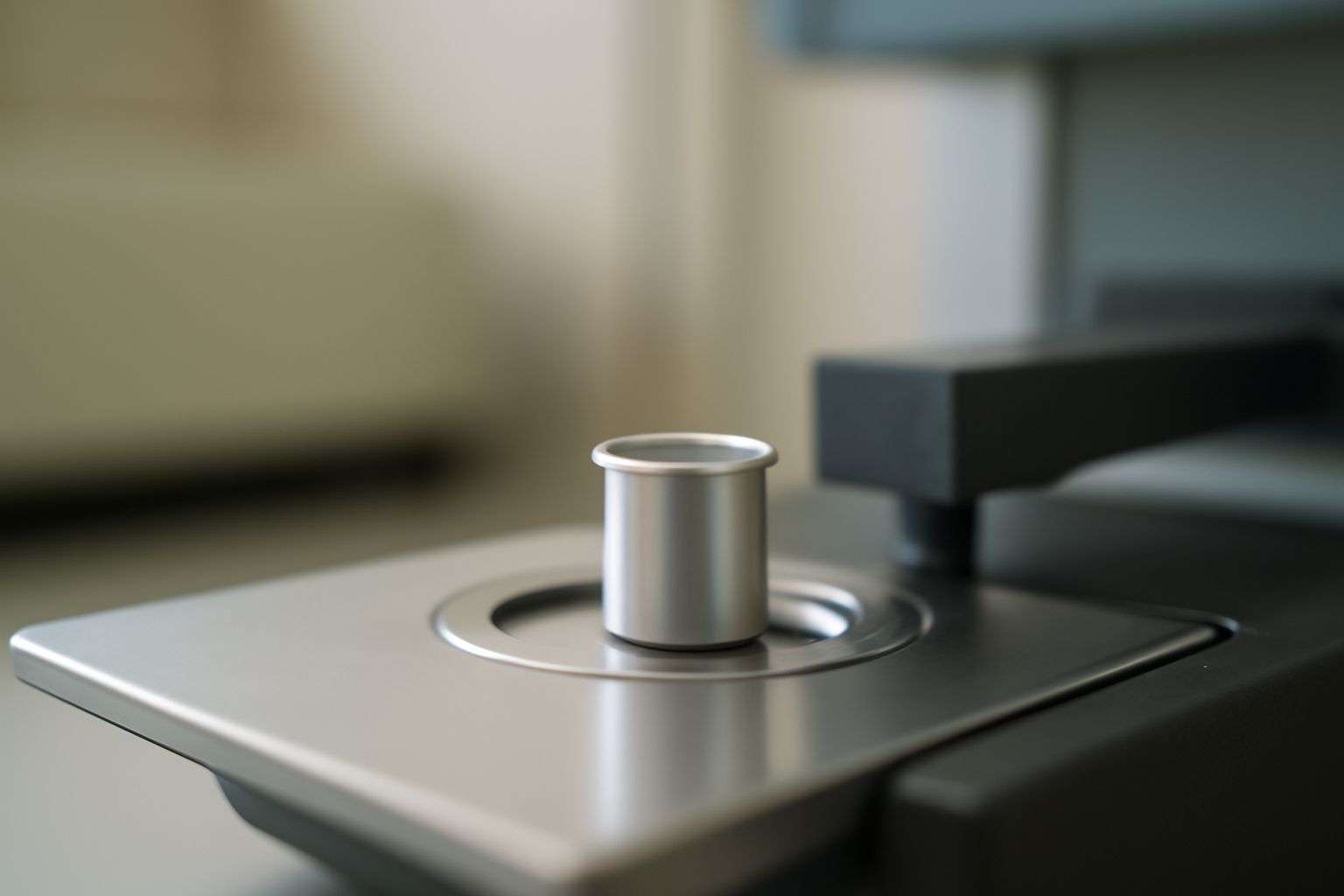
I have seen labs save both time and sample material once their team starts using the right DTA crucible. The search for the best product leads to better data and fewer failed tests. Reliable sourcing also makes lab routines smoother and less stressful. Every lab can benefit from making the right choice upfront and avoiding common supply errors.
What are the key factors to consider when buying a DTA crucible?
A low-quality crucible can break or cause data errors. Every lab needs the right mix of reliability, material strength, and exact size for its thermal tests.
Choose a DTA crucible with the correct material, size, and heat resistance for your thermal analysis. Make sure it matches the specifications of your instrument and the target temperature range.
Key Factor | What to Look For | Reference |
---|---|---|
Material | Use high-purity metals like aluminum or platinum for better chemical stability and heat transfer | crucible |
Size & Fit | Check compatibility with sample mass, volume, and your brand of instrument | laboratory instrument |
Heat Resistance | Review maximum working temperature for both the crucible and the sample | thermal analysis |
Supplier Support | Look for detailed product specs, brand cross-reference, and technical advice | technical support |
I remember once choosing a cheaper pan because of budget pressure. The results were not good. Now I always check for full technical details and supplier guidance.
Where to purchase high-quality differential thermal analysis crucibles?
Not all suppliers offer the same quality or support. Buying from the wrong place risks delayed shipments and mismatched products.
Look for specialized suppliers who offer detailed product listings, clear compatibility charts, and fast global shipping. Trusted online stores and direct factory brands are strong options for labs.
Supplier | Why Choose | Reference |
---|---|---|
Direct Factory Stores | Lower cost, technical support, and verified product compatibility | manufacturing |
Online Scientific Marketplaces | Wide selection, brand options, and user review feedback | e-commerce |
Specialized Lab Suppliers | Industry focus, support for instrument-specific questions, and tailored logistics | laboratory equipment |
I have placed orders both with large resellers and direct suppliers. I trust suppliers like REDTHERMO because their technical answers are quick and they list all the instrument models their pans support.
How to ensure the DTA crucible is compatible with your equipment?
A mismatched crucible may not fit the machine or may cause errors in sensitive temperature readings. This problem leads to lost material and failed tests.
Check all size, shape, and closure specs. Use brand and model match tables, ask the supplier for advice, and confirm part numbers before buying. Good suppliers provide fast answers for compatibility questions.
Compatibility Checklist | How to Verify | Reference |
---|---|---|
Instrument Model | Match DTA crucible to the model number of your analyzer | thermal analysis |
Size & Dimensions | Use detailed size charts and measure sample holder space | laboratory instrument |
Closure Type | Choose open, sealed, or vented pans for specific sample needs | seal |
Technical Support | Contact supplier for quick Q&A and documentation | technical support |
Once I ordered a batch that did not fit our Mettler Toledo unit. That mistake led to extra costs and delays. After that, I made sure every order matched part codes and specs exactly.
What are the most common issues when purchasing DTA crucibles?
Labs sometimes face late deliveries, supply shortages, and low-grade materials. These issues affect the quality of data and slow down research.
The most common issues are unexpected size differences, poor material purity, missing compatibility info, and a lack of technical support from sellers. These problems hurt testing integrity and boost costs over time.
Common Problem | Impact on Lab | Reference |
---|---|---|
Incorrect Size | Leads to leaks, test failures, or equipment damage | dimensional tolerance |
Poor Metal Purity | Causes thermal drift and false signal results | alloy |
Slow Shipping | Disrupts testing schedules and delays reporting | supply chain |
Compatibility Errors | Creates extra costs from repeat orders and lost samples | laboratory equipment |
After we improved our supplier review process, I noticed lab downtime dropped. We tracked every issue to avoid repeat errors and worked with suppliers who gave fast answers.